Point of Operation Safeguards, Devices and Controls
Machine safeguarding refers to a wide range of devices on or near equipment that protect people from harm. Production Resources offers a complete line of ANSI and OSHA compliant machine guards and safeguarding devices, including power press clutch/brake controls, light curtains (presence sensing devices), sliding barrier devices, barrier guards, pull outs, restraints, riveter guarding devices, safety mats, safety/die blocks, and area/perimeter guarding devices.
We can help you select the right machine safeguarding for your power press, press brake, fabricating equipment, coil line, and/or robotic work cell. Proper safeguard selection is vital not only to operator safety but productivity as well. It’s important do a risk assessment: properly identify the hazard, how the operator and others are exposed, frequency of exposure, and the nature and probability of injury. Operator interaction with the machine, stroke/cycle initiation means, part loading/unloading procedures, stopping performance, and passersby exposure must all be considered.
Control system design must also be considered as part of any safeguarding solution. Adding a safeguard to a machine with a poorly designed control or one non-compliant with safety standards is dangerous. When a machine safeguarding system sends a stop command, the machine control system must respond instantly. A control failure must be recognized such that safety is not compromised. Safety systems are often compromised by poor maintenance, bypass schemes, or other system alternations. When a control system is modified, changes – especially electrical wiring – must be done safely and documented.
Our Application Engineers have working knowledge of the ANSI power press standards (B11.1) (B11.19), hydraulic press standards (B11.2), and press brake standards (B11.3) as well as OSHA regulations 1910.212 and 1910.217. They can help you determine if your equipment is in compliance and recommend the safest and most productive machine guarding solutions.
See our technical resources articles on power press and press brake safety:
Application Guideline for Proper Use of Light Curtains
Press Brake Alternative Guarding Methods
Power Press OSHA/ANSI Control Compliance
Light Curtain Application Issues – “Walk Thru Hazards”
Full Revolution Clutch Mechanical Power Presses
Guidelines for Safety Distance Calculations When Using Light Curtain Blanking Functions
The S3000 Safety Laser Scanner
Wintriss SmartPAC Brake Monitor Capabilities
Productivity, Safety, and Ergonomic Considerations for Hand-fed Presses
PRI distributes major brands such as: Wintriss, Protech, Miller Edge, Positive Safety, Rockford Systems LLC, and HTM Electronics.
Wintriss OSHA/ANSI Compliant Power Press Clutch / Brake Press Controls
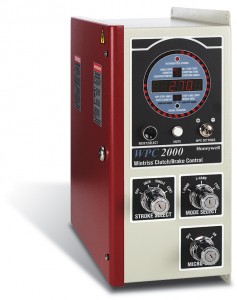
The Wintriss 1000 and 2000 Clutch / Brake controls both meet or exceed all ANSI B11.1 and OSHA 1910.217 regulations, including control reliability. Press and floor console models are available with or without motor controls built to your exact specifications. Integral brake monitors to check the stopping performance and a host of other features are available including optional integration with the Wintriss SmartPAC2 press automation control system.
Light Curtains
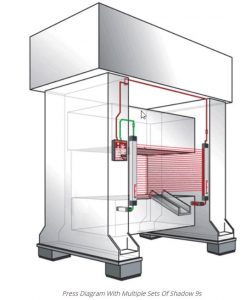
The Wintriss Shadow® 9 is the latest safety light curtain from the Wintriss. Wintriss has been building the Shadow® light curtains for the toughest applications for more than 45 years with 50,000 installed. Shadow 9 is designed to handle the rigors of the pressroom, including severe shock, mechanical abuse, and stamping lubricants.
Die Doors
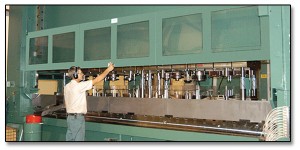
Pax die doors are point of operation safeguarding devices for mechanical power presses. They are best suited to coil fed and/or automatic operations and prevent the operator from entering the work area while the press is running as the doors are interlocked with the press stop circuit. Additionally, they contain fluids and flying objects.
Pax die doors help you maintain a clean and safe workplace. Models are also available to help you control sound pressure levels.
Safety Mats
Safety mats, also known as safe guarding mats, are presence sensing devices typically used with fabricating machines, supplementary guarding, and for area guarding applications. They provide additional safety for passers-by, helpers, and primary operators.
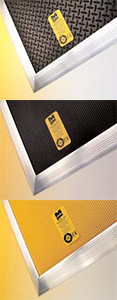
Perimeter and Area Guarding Devices
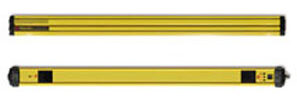
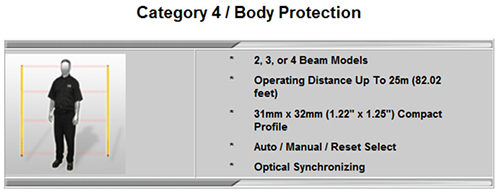
S3000 Safety Laser
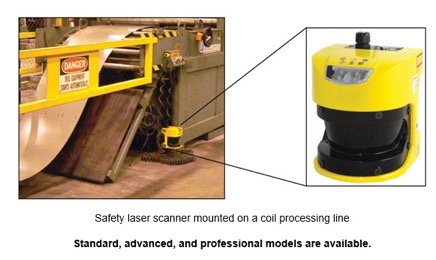
The S3000 safety laser scanner is a safeguarding device that meets industry OSHA, ANSI, UL, IEC, and EN safety standards. Its use is for difficult to guard category 3 applications that may cause injury but will not result in death, cause amputation, or other catastrophic injury. It is designed for indoor hazardous area and machinery protection, access protection, guided vehicle protection, robot stations, and irregular shaped areas. The safety laser scanner is an optical sensor that scans its surroundings in two dimensions using infrared laser beams. It sends out very short pulses of light and measures the time it takes to reflect back (time of flight measurement).
Up to eight (8) programmable warning fields and protective fields are available, depending on which scanner model is chosen. Each warning field has a non-safety output that can be interfaced to a light, PLC, display, etc., to warn of impending encroachment of a protective field. Any interruption to a protective field will cause the OSSDs to drop and initiate a stop signal to the machine control system (machine primary control elements–MPCE).
The programmable feature of the scanner eliminates the need to reprogram the scanner every time something changes within the field. For example, if something is regularly moved in and out of a field, then multiple fields can be programmed to accommodate the changes. A static input allows for a selector switch or PLC to be used to change the field sets as needed.
WireCrafters Perimeter & Area Barrier Guarding Devices
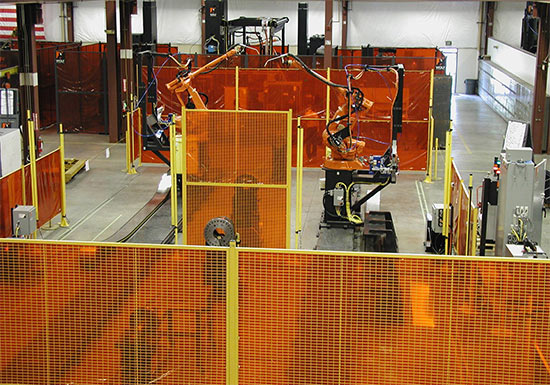
Physical barrier guards should be considered as a machine safeguarding solution where frequent access and/or maximum visibility to the operation or process is not of major importance. Often a barrier guard may be combined with other safeguarding solutions, such as presence sensing devices, to create a more flexible and complete guarding solution.
We offer woven and welded wire physical barriers from WireCrafters. These barriers are a practical, easy to use/maintain, affordable guarding system for robotic cells, automated work cells, and general-purpose perimeter guarding applications.
PRI can help you configure a guarding system to meet your specific needs. We have experience in configuring practical safeguarding solutions without harming productivity.
Press Brake Guarding
Protech Systems integrates Eagle Eye light curtains with control systems designed specifically for use with press brakes. Systems are available to work with friction clutch treadle operated machines, air clutch machines, and hydraulic machines. Programmable beam blank-out features allow the light curtain to accommodate bending profiles in sync with CNC back gauges for box, tray, or other complex bending applications.
The light curtain ignores objects of 3/8” or less so flat sheet air bends are easily accomplished. For box forming, tray forming, and similar operations where the part flange interrupts the light curtain, the programmable beam blank out feature is used.
Small short part forming is accommodated using a stroke stop feature.
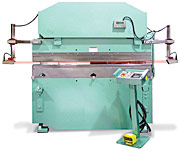
These systems range in price from $7,500 to $15,000 depending on features and whether provision for new motor controls are required.
LazerSafe press brake guarding is specifically designed for use with fast stopping hydraulic press brakes where it’s necessary to hold short work pieces close to the tooling. This system is applicable to newer press brakes with “creep speed” provisions.
Typical LazerSafe systems start at $13,000 installed.
Safety Blocks
Safety blocks are designed to prevent accidental die closure during press setup and maintenance. Constructed from lightweight extruded aluminum or magnesium our safety locks are available in fixed and adjustable styles to handle a variety of static loads.
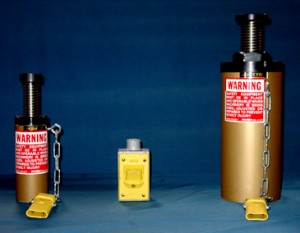
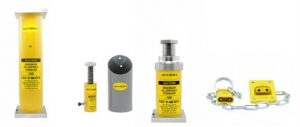
Welder & Riveter Safeguarding Devices
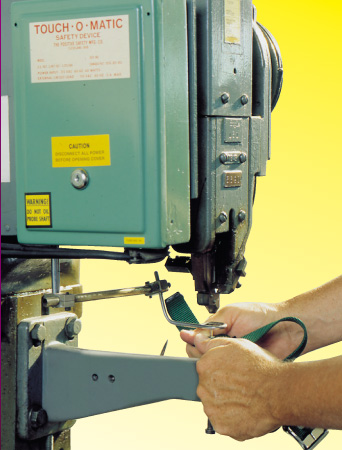
Drop ring safeguarding devices provide economical, simple-to-understand-and-use, reliable protection for an operator’s finger and hand protection while using riveter guards, spot welders, staking presses, or similar devices. These devices employ a mechanical assembly with a “drop ring” that gravity falls around the point of operation before the machine cycle.
The SOFT TOUCH Pinch-Point Safety System passive machine safeguarding system uses electrical continuity measurements to determine if an operator’s hands or fingers are in danger. If a hazard is identified, the system prevents the machine from delivering its full force. SOFT TOUCH is easy to use and requires no operator adjustments.